自從氫能被總理在政府工作報告上提及后,氫燃料電池行業近來貌似如火如荼,但是膜電極作為燃料電池電堆最關鍵的一環,國內會存在哪些問題呢?與國際上的領先企業相比差距大嗎?
以下是困擾中國膜電極發展的主要的幾個問題。
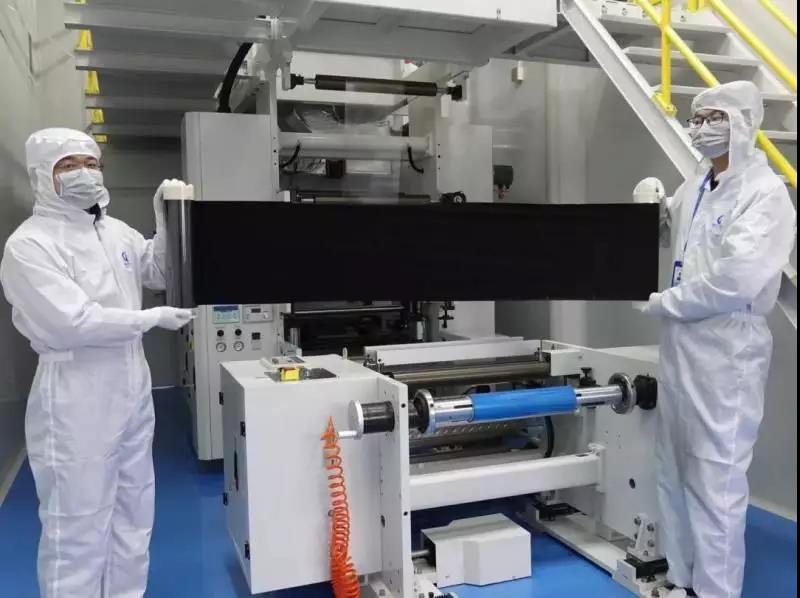
蘇州擎動膜電極
一、關鍵材料問題
催化層
質子交換膜燃料電池中膜電極組件(MEA)是整個電池的核心,目前MEA中的催化層絕大部分采用鉑(Pt)作催化劑,在EMA中鉑催化劑大多為負載型催化劑,這些負載型超細鉑催化劑具有金屬顆粒小、分散度高、活性表面積大和表面能高的特點,因而具有獨特的催化性能。
在燃料電池中鉑作為催化活性中心,其含量直接影響電極的電催化性能和電池的性能及成本。鉑是貴金屬,資源有限,其成本不會隨著規模的擴大而成本降低,甚至可能上升。
因此,需要從技術層面盡可能地降低Pt用量,同時保證膜電極壽命不受影響,這是一個難點。
能鏈采訪了武漢理工氫電的總經理田明星,他介紹說目前很多研究機構都在研究無鉑(Pt)技術,如武漢理工氫電的技術支撐方武漢理工大學也有許多教授在做非Pt催化劑研究。
武漢理工氫電認為,目前非Pt催化劑在車用方面,商業化的可行性比較低,但非Pt是未來理想的目標,但短期內在商業化產品上沒有想象中那么快,所以短期內還是以低Pt作為技術路線。低鉑和無鉑催化劑是未來技術發展方向。
目前國內技術水平下催化層中的鉑載量為0.5g-0.8g/kw,而國際領先的企業已經能夠做到0.3g-0.5g/kw,美國能源局的目標是,到2020年鉑用量降至每千瓦0.125g。
擴散層
在質子交換膜燃料電池中,氣體擴散層主要作用是為參與反應的氣體和生成的水提供傳輸通道、支撐催化劑。
作為膜電極關鍵組成材料之一,其國產化突破與量產,對中國燃料電池成本降低與推廣應用具有重要價值。氣體擴散層由基底層和微孔層組成,其中基底層材料大多是多孔炭紙或碳布,微孔層通常由導電炭黑和憎水劑構成。
目前全球碳紙/碳布生產廠家較少,供應商主要為日本東麗、德國西格里集團、日本JSR、加拿大Ballard、臺灣碳能等。
其中,東麗占據較大的市場份額,我國對碳紙的研發主要集中于中南大學、武漢理工大學等高校。
中國大陸氣體擴散層量產技術還是空白,主要原因是氣體擴散層的石墨化工序需要2000°C以上的高溫,但高溫爐技術尚未掌握。
質子交換膜
質子交換膜的性能直接影響燃料電池的穩定性和耐久性。
質子交換膜的主要作用有兩個:一方面為電解質提供氫離子通道,一方面作為隔膜隔離兩極反應氣體。此外,質子交換膜還需要對催化劑層起到支撐作用。
質子交換膜類型主要包括全氟磺酸質子交換膜、非全氟化質子交換膜、無氟化質子交換膜、復合膜以及高溫膜。目前,最廣泛應用的質子交換膜為戈爾的select膜。
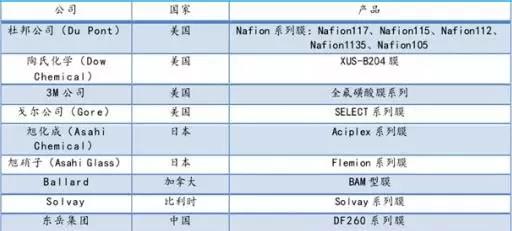
國內外主要質子交換膜生產廠家及產品( 來源:國家統計局等公開來源)
國內新源動力和東方電氣近來推出的燃料電池電堆都采用了國外戈爾公司的GORE-SELECT?質子交換膜。(戈爾是全球領先的質子交換膜燃料電池技術供應商。GORE-SELECT?質子交換膜成為滿足汽車嚴苛應用的標準,這款質子交換膜早已應用于其他的商業燃料電池汽車,如豐田的MIRAI和本田的CLARITY FUEL CELL。)
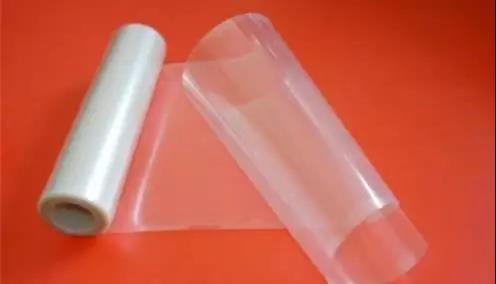
東岳集團全氟磺酸質子交換膜示意圖
目前國內能夠批量化供應質子交換膜的企業只有山東東岳,其他企業多數都在研發或者小批量試產階段。
二、制備技術問題
膜電極技術目前經歷了幾代革新,大體上可以分為熱壓法、CCM法和有序化膜電極三種類型。
第一代的膜電極制備工藝主要采用熱壓法,具體是將催化劑漿料涂覆在氣體擴散層上,構成陽極和陰極催化層,再將其和質子交換膜通過熱壓結合在一起,形成的這種膜電極稱之為“GDE”結構膜電極。
采用熱壓法優點:膜電極的通氣性能良好,制備過程中質子交換膜不易變形。
采用熱壓法缺點:催化劑涂覆在氣體擴散層上,易通過孔隙嵌入到氣體擴散層內部,造成催化劑的利用率下降,并且熱壓粘合后的催化劑層和質子交換膜之間粘力較差,導致膜電極總體性能不高。

第二代的膜電極制備技術是催化劑直接涂膜技術(見上圖),具體是將催化層直接涂覆在質子交換膜的兩側,再通過熱壓的方式將其和氣體擴散層結合在一起形成“CCM”結構膜電極。
該技術提高了催化劑的利用率,并且由于使用質子交換膜的核心材料作為粘結劑,使催化層和質子交換膜之間的阻力降低,提高了氫離子在催化劑層的擴散和運動,從而提高性能,是目前的主流應用技術。
但是第二代膜電極制取方法還存在著反應過程中催化層結構不穩定,Pt顆粒易脫落的問題,影響著膜電極的使用壽命。
針對該現象,各大研究機構結合高分子材料技術及納米材料技術,向催化層的有序化方向發展,制成的有序化膜電極具有優良的多相傳質通道,大幅度降低了膜電極中催化劑Pt的載量,并提升了膜電極的性能和使用壽命。
膜電極結構的有序化使得電子、質子氣體傳質高效暢通,對于提高發電性能和降低PGM的載量提供了新的解決方案,有序化膜電極是下一代膜電極制備技術的主攻方向。
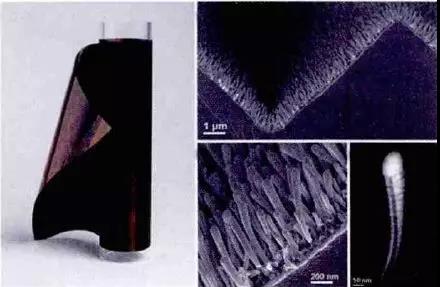
3M公司有序化膜電極及NSTF催化劑層形貌
目前國內企業采用的主要是CCM生產工藝,與國外相比,國外膜電極制備技術已經開發多年,甚至3M公司已經開發出了可量產的有序化膜電極技術,國內膜電極制備技術目前還有很大的提升空間。
國際膜電極的主要制造商是GORE,莊信萬豐,Ballard,Greenerity等。
國內膜電極供應商主要是武漢理工新能源,其產品主要供應美國PlugPower公司。大連新源動力的膜電極產品主要是為上汽的發動機配套。
現階段來看,國產膜電極性能與國際水平接近,但專業特性上如鉑載量等性能與國際水平還有一定差距。
三、成本問題
產業化問題——現在要做出膜電極的樣品,對于很多國內企業l來說并不是一件非常難的事情,難的是怎么實現幾十萬、幾百萬件的批量生產,生產的一致性、生產工藝水平高低都是會影響產品性能和成本的。
為了實現核心技術的自主可控,自2015年以來,全國各地紛紛出臺政策,鼓勵企業發展燃料電池產業,在產業環境與政策利好雙重支撐下,中國的燃料電池產業鏈上的企業從無到有,從下游向上游進發。
而在《中國制造2025》里面更是提出,到2030年,要實現燃料電池高品質關鍵材料、零部件國產化和批量供應,燃料電池膜電極成本≤50元/kW。
(來源:能鏈)